Boris Sedacca, editor of Electrical Times magazine, published by Voltimum Media Partner Highbury Business Communications, looks at the practical application of feedback control loops – in, for example, building control:
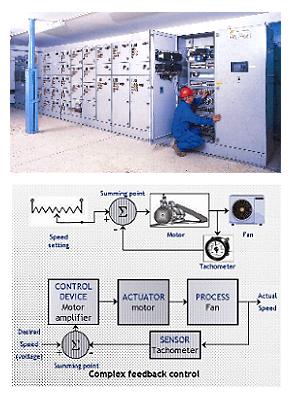
Practical, real-life examples are usually a little more sophisticated. In a HVAC system for example, several sensors might provide feedback to the system. Where there are several feedback elements, a proportional, integral, and differential (PID) control loop will often be used.
Taking a mechanical example, if speed is the proportional term and expressed in metres per second (m/s), then acceleration is the difference in speed over time or differential term, expressed in metres per second every second (m/s2). Distance is the integral term and expressed in metres (m).
A motorcar will typically show road speed (speedometer), engine speed (tachometer) and total distance (mileage counter). The first two are proportional terms, showing values from zero to a maximum, while the latter is an integral term showing a value that only increases, never returning to zero (unless a mechanic tampers with it of course.)
Some cars may have an accelerometer fitted, which will show zero at standstill or constant speed, and acceleration (increasing speed) or deceleration (decreasing speed) either side of zero.
In a HVAC system, motor speed will translate to air pressure, whose differential is flow and whose integral is volume. For example, Siemens' Micromaster inverter for HVAC has six programmable digital inputs, two analog input/outputs, and two digital outputs.
Feedback signals:
The Integrated PID controller allows accurate control of flow, pressure or temperature by direct connection from external sensors. Feedback signals can be via 0-10V, 0-20mA, or 4-20mA signals. The loop gain of the control system can be adjusted in PID terms.
A PID controller examines signals from sensors placed in the system, called feedback signals. When the feedback signal is received, it is compared with the desired value, or setpoint, and a calculation is made of what the necessary response is in order to make the feedback signal match the setpoint.
The controller is usually either a separate device, part of an OEM device such as an air handling unit (AHU) or pump controller or a piece of software internal to the building management system (BMS).
The Danfoss VLT 6000 HVAC inverter has a PID controller integrated in the software.
In many applications it is required to maintain a specific difference between two feedback signals. According to Danfoss, this is normally done with an expensive outstation monitoring two feedback signals and controlling two independent actuators.
This kind of control is often used in AHUs, where a fixed difference in flow is applied between supply air and return air. The VLT 6000 can control the return air fan speed to maintain this difference.
Another use of this function is when a differential pressure (DP) value is to be maintained across a heat load in the heating system. This is normally done using a differential pressure transmitter.
With the VLT 6000, two standard transmitters can be applied and if difference is programmed in one of the parameters, the PID controller will react as if a differential pressure transmitter was installed. It is possible to program the correlation between the voltage and current input and what the feedback in units should be.
Apart from air pressure and flow, a PID will also provide control of heating coils. The new Canary Wharf offices of Morgan Stanley Dean Witter rely on Saftronics motor control centres (MCCs) to control building services.
The contract value of over £200,000 was for eight Form 4 type 2 LV Switchboards and MCCs with front access and top cable entry. A mixture of starters and power feeders were provided in each MCC for the control of chilled water pumps, air conditioning vent heating thyristor, PID controlled coils, office air supply fans, office supply fan humidifiers, office and car park smoke extraction fans, stair pressurisation fans, lift power supplies and car park roller shutter door supplies.
Motor control:
Each MCC was supplied with its own BMS to interface with an overall BMS for the building. In addition Saftronics supplied nine 63A and two 400A automatic power source changeover units, which were also monitored by the BMS.
The purpose of HVAC control systems is to keep people comfortable within an enclosed space, achieving desired temperature, humidity, pressure, radiant energy, air motion and air quality.
One of the software packages covered in last month's panel building feature for modelling and simulating control systems was Visual Solutions' VisSim. Nebil Ben-Aissa of Johnson Controls has used VisSim to model a Variable Air Volume (VAV) HVAC system that controls the temperature inside a space by modulating the amount of air supplied to it.
The air handling system is the primary HVAC system in most building HVAC installations. This system, which is hidden from most building occupants, is the main system that delivers conditioned air to the entire building.
The main responsibility of the air handling system is to supply the building with fresh and conditioned air, then exhaust it from contaminated and carbon dioxide air. Most air handling equipment is located on building rooftops.
Variable air volume:
The air handling equipment consists of outside air dampers, mixed air dampers, heating coils, cooling coils, and supply air fans. The air handling controls consist of the electronic control hardware that sequences the operation of the air handling system. The PID controller monitors the room temperature and controls the VAV damper position. Carrier Corporation, a division of United Technologies Corporation, is one of the largest manufacturers and distributors of Heating, Ventilating, and Air Conditioning (HVAC) equipment worldwide.
For more than five years, Carrier has been using VisSim to model, simulate, and validate product designs ranging in scope from single zone air conditioners to hundred-ton chillers used in hospitals, university campuses, and office complexes.
Carrier uses VisSim to develop and test its electronic controls and depends on the resulting shortened development times to continually merge new technology into its products. Products which would have taken two to three years to develop in the past are now routinely completed using VisSim in less than one year.
A recent VisSim modeling effort conducted by Dr. Fred Cogswell, senior scientist at United Technologies Research Center, focused on the development of a reciprocating chiller model for simulating faults. The reciprocating chiller consisted of two refrigerant circuits, each with the following components:
- One to four reciprocating compressors in parallel to compress the refrigerant vapour.
- A water-cooled or air-cooled condenser to remove heat from the high pressure refrigerant and condense it to liquid.
- A stepper motor controlled expansion valve to meter the refrigerant flow as it goes from high to low pressure.
- An evaporator to transfer heat from the chilled water to the refrigerant, thus boiling the refrigerant to vapour while providing cooling.
The model, which consisted of approximately 6,000 blocks, performed a dynamic simulation of the chiller system tracking the migration of refrigerant between components as well as the control interactions.
Contacts:
www.sea.siemens.com/drives/product/gpd/eco/drecoov.htm
www.danfossdrives.com/products
www.saftronics.co.uk/pages/projects/canarywharf.htm
www.esparkinfotech.com/vissim/tutorials/HVAC.PDF
www.vissim.com/apps/carrier.htm
www.server1.xpedio.carrier.com/idc/groups/public/documents/marketing/830-077-020199.pdf
This article was originally published in Electrical Times magazine (issue August 2004) by Highbury Business Communications - a Voltimum UK Media Partner.
Contact: Boris Sedacca
Electrical Times
Highbury Business Communications
Nexus House, Azalea Drive, Swanley, Kent BR8 8HY
Tel: 01322 660070
Fax: 01322 616376
Email: [email protected]
Web: www.hhc.co.uk
And: www.electricaltimes.co.uk