In recent years, there has been increasing concern in the industry regarding PEN faults—a specific type of network fault with potentially lethal consequences.
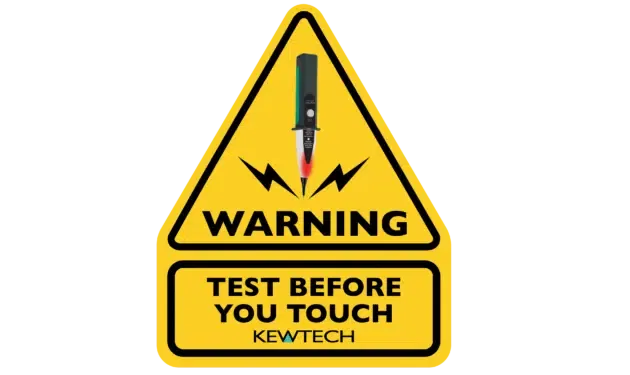
While the rise in PEN faults is being acknowledged and investigated, it’s important to note that these are not the only way that hazardous situations, including Touch Voltage and Diverted Current flow, are created.
In particular, there has been an increasing number of incidents where engineers have come into contact with live metallic parts (e.g., metal casings or equipment) during installation or maintenance activities. These contacts can and have led to fatalities.
Touch Voltages and Diverted Currents
Touch Voltages: This occurs when there is a fault in the system that results in no return path for current (i.e., due to a broken or disconnected earth or neutral, combined with other faulty wiring). As a result, metallic parts (such as a distribution board, boilers or control panel) that are connected to the electrical earth could be raised to a dangerous potential.
Diverted Current: This is a more complex fault, where the current may flow through unintended paths (e.g., through earth or neutral conductors). Even though the circuit might appear to be functioning normally, diverted current can present serious dangers.
Let’s have a look at a couple of potential scenarios you may come across…
Scenario One: The fault is hidden, and the current appears to be flowing correctly in the system, as everything is working, but when measured, it is found that the current is flowing through earth conductors. This can be detected only by measuring multiple points across the earthing and neutral conductors in the installation, (current will always follow the path of least resistance). If not detected, disconnecting cables could break the return path and present a touch voltage hazard.
KT5 open jaw current & voltage tester
Scenario Two: When we isolate a circuit and prove it dead, everything should measure as being at zero potential; however, where we have multiple cables under terminals within that isolated circuit, we may also have current still flowing through the return path or via the neutral, either through cross circuits or faulty wiring. If proper checks are not performed, engineers could potentially break these return paths when disconnecting cables, creating dangerous touch voltages in the system.
Prevention Tip: Use a clamp meter to check current flow, especially when multiple cables are connected to the same terminal. This can help prevent introducing a new hazard when disconnecting cables.
Kewtech’s KT5 open jaw current and voltage tester is an ideal safe isolation tool equipping you with non-contact voltage indication, single and two pole voltage indication and current measurement all-in-one.
Issues with Current Safe Isolation Procedures:
The current safe isolation procedures in place often do not specifically account for or test for touch voltages and diverted current. Even though the best industry practices for safe isolation and proving dead are followed, these two specific hazards are often overlooked.
The proving dead process usually involves opening enclosures or testing electrical terminals to confirm that the equipment is not live. However, this step can be potentially lethal if there is already a touch voltage present.
Test Before Touch – The Missing Step:
The concept of ‘Test Before Touch’ is well-established and often taught to engineers. However, it’s usually focused on high-voltage equipment, and not before entering or touching low-voltage equipment like distribution boards, control panels, pipework, and appliance casings (e.g., boilers or motor casings).
In practice, engineers may not always adhere to this guideline, especially when handling parts of the installation that seem to be disconnected or “dead.” They may neglect to check if there is a touch voltage or diverted current present.
Testing Equipment for Hazard Detection:
Non-contact voltage indicators (such as the KEWSTICK DUO) and single-pole voltage detectors Kewtech’s KT1700) are often used as tools to check for the presence of dangerous voltages, though these only give us an indication that a lethal voltage may be present. Crucially, in the case of a PEN fault or similar, all conductors may be at the same potential, so when measured using a two-pole BS EN 61243-3 voltage indicator, these tools might not effectively identify the risk. In such a scenario, a single-pole device would at least give us that potentially life-saving indication.
KT1700 single pole voltage indicator
Will our industry adapt?
Industry guidance on safe isolation and proving dead circuits do not typically account for checking for these hidden hazards, as part of the safe isolation process.
There is the urgent need therefore to improve safety standards and include testing protocols specifically for touch voltages and diverted current, as part of the standard safe isolation protocol.
It is critical that electricians and engineers are equipped with the correct tools designed to detect these issues. The need for a BS EN 61243-3 voltage indicator and proving unit should be accompanied by a single pole detection device and an amp meter as a minimum.
With this, it is essential that training programs ensure they are updated to include awareness of these risks and proper techniques to mitigate them.
Summary:
The industry’s focus on PEN faults is undoubtedly important, however, it shouldn’t overshadow the fact that deadly electrical hazards like touch voltages and diverted current are present in many installations without PEN faults. These types of faults are often not checked during routine isolation procedures, leaving engineers at risk. By updating safety protocols, ensuring proper training, and using the right test equipment, these risks can be minimised, leading to safer practices in the field.
And remember… Test Before Touch!
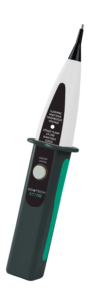
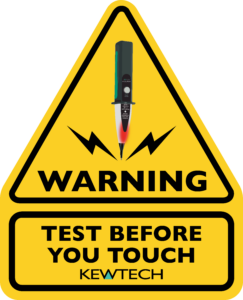
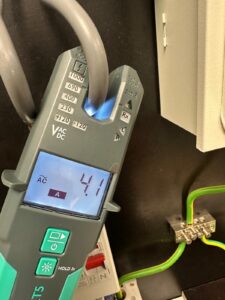
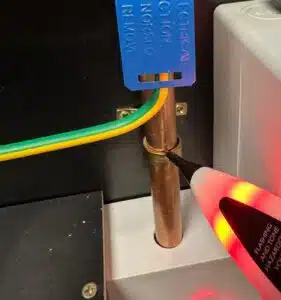
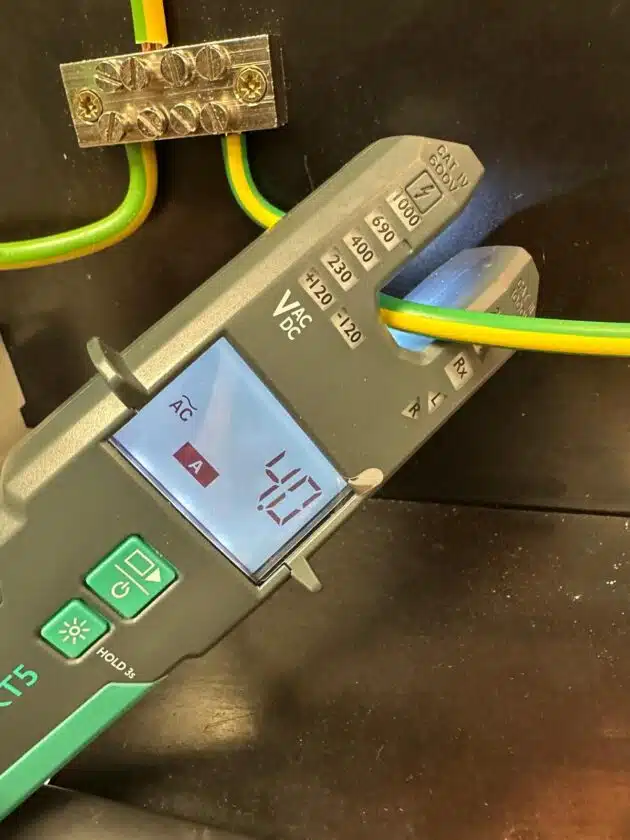