Torque screwdrivers have been available for some years, but very few electricians use them. Electricians are typically more likely to use a torque wrench on larger conductors (if at all), such as those found on Low voltage (LV) transformers or switchboards, but not on branch circuit connections. This is changing, in part because of wider torque screwdriver availability and reducing cost, but mainly because legislation, insurers and safety constraints increasingly demand it, as James Hunt reports:
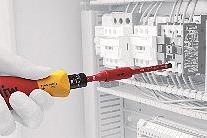
The two essentials in making and maintaining reliable electrical connections are:
- Start with clean contact surfaces (a function of cleaning procedures)
- Apply a high load (by torqueing the fasteners).
In any electrical circuit, vibration, fatigue and age can cause the loosening of electrical connections, whether screwed or bolted. Essentially, all electrical connections will tend to follow a path towards failure over time. If not found and repaired (or re-tightened), such failing connections can lead to faults. A loose or corroded connection increases resistance at the connection, which in turn results in an increase in heat.
Connections that are too loose can also cause arcing, whereas over tightening does not improve reliability but can cause the bolt or screw to cut through the wire and also damage the connection (or even cause early screw failure). It can even break conductor strands. So over-torqueing and under-torqueing - such as invariably happens to some extent when tightening is done by hand - are both potentially risky.
Detecting and correcting failing connections before a fault occurs helps avoid fires that can occur. It can also avoid expensive electrical equipment downtime.
It is reported that insurance companies now realise the importance of torqueing, and apparently this is now an early questions in the event of a claim. However, while most manufacturers do specify torque settings for important fasteners, until recently at least, few have published these settings with their electrical equipment. In general, however, if there is a torque specified, it should be adhered to.
To date (and apart from large bolted low voltage joints in switchpanels and the like), it seems that only consumer unit, circuit breaker and a few time-clock manufacturers specify specific torques – or so some electrical installers think! See the information about Neweys Online (link below) and the excellent list of torque settings actually provided.
Fluke says that guidelines provided by the InterNational Electrical Testing Association (NETA) emphasises that when the difference in temperature between similar components under similar loading exceeds 15°C, immediate repairs should be undertaken. Of course, one way to help avoid problems in the first place is to ensure that bolted or screwed joints are tight to start with. One of the best ways to achieve this (and the most commonly used) is to employ a torque wrench (for bolted joints) or a torque screwdriver (for screwed joints).
Also, studies have indicated that while electrical installers are slightly more likely to over-tighten connections than non-electricians, they are no better at achieving a proper connection than somebody having no experience as an electrician.
It is for all these reasons that Regulations 134.1.1 and 510.2 in BS7671:2008 (First Amendment) require electrical equipment to be installed in accordance with instructions provided by the manufacturer. Product installation must adhere to manufacturer specification, including the torque settings. It is, therefore, now necessary to check that all connections are tight, which means that electrical installers should check torque settings for connection tightness at consumer units (where these are manufacturers' specific instructions).
While typical electrical systems are designed with considerable safety factors built-in, and circuits are rarely fully loaded, this is no justification for ignoring basic installation instructions.
Beware!
However, torque can be misleading. For example, if a bolted or screwed connection has been frozen through corrosion, arcing or any other reason, the torque needed to un-tighten it (or tighten it) may be insufficient to provide the correct load on the joint. Take care that all joints to be tightened are clean and that the fasteners work smoothly with little friction (until becoming tight).
Torque screwdrivers:
Engineers have been buying torque screwdrivers for years – and they cost between £80 and £300.
Torque screwdrivers come in a variety of designs all allowing screws to be tightened in a safe and reliable way to a specific degree of tightness - usually measured by the torque (twist) applied - and also clearly indicating that torque, usually in units of Newton metres (Nm). Some designs can even record the torque for each fastening. Some will sound an alarm if a screw is tightened beyond a certain torque, which can cause connections to fail mechanically.
No single torque tool covers the full range of possible torques, so it is important to select for the right torque range. There are various types, including clutch, cam over, cushion clutch and auto-shut off types, plus manual, electric, cordless and pneumatic variants - electric and pneumatic types are most suited to manufacturing rather than installation and repair.
Most torque screwdrivers are available with an assortment of tips to fit various sizes of straight-slot, Phillips or other types of screw heads. Set-screw connectors are common in electrical equipment, including panelboards, switchboards, and meter bases - these too are accommodated. Some may also come with sockets to fit over smaller sized nuts.
Quite apart from legislative demands and safety benefits, the latest torque screwdrivers are very simple to use, enabling electrical installers to simply nip up with any conventional screwdriver. Once the consumer unit is full, just set the torque on the torque screwdriver and fully tighten all the terminals at once until the driver makes the clicking sound that all is well.
Of course, a torque screwdriver is another cost (though not too much), but a little extra cost now can save a great deal of money and worry (and possibly legal action) if a fire occurs because of an incorrectly tightened connection.
Electricians have been buying VDE insulated screwdrivers for years and wholesalers mainly stock these VDE approved tools. Now the two can be combined. Wiha is the German tool specialist company that first combined the two fields - torque accuracy and VDE security and ended up with what is called the ‘Ultimate Electricians Screwdriver’ - the TorqueVario VDE. Schneider Electric and Wiha are the first organisations to market these screwdrivers.
The NICEIC and ECA assessors/auditors have all been trained on the product and can answer questions that their members may have during site visits.
A torque screwdriver should be checked for calibration once a year and a new certificate supplied. Torque screwdriver kits cost users around £110 and the torque handle is around £80 of that. That handle has a life of 3-5 years as is also a piece of calibrated test equipment. The blades cost about £5 each - the same as a decent screwdriver.
For the future:
Torqueing electrical connection fasteners will become ever more important. Sales of VDE torque screwdrivers are growing exponentially. The cost of a kit is the same as a tank of diesel. Moreover, the enormity of the smart meter rollout has prompted energy suppliers to evaluate their risks and arm their installers with torque screwdrivers. If the UK is to fit 26 million smart meters over the next nine years, that means 8000 units per day will be installed. These will need to be installed correctly so that the fire statistics are not adversely affected.
Neweysonline (as already stated) has collated all the torque settings from the major manufacturers and put them in one place for users to go to and print. Go to www.neweysonline.co.uk/neweys/pdf/WI00_Torque_Setting_Data_Technical.pdf for this highly useful information.
For further information about torque screwdrivers (as well as other topics), please see the other articles in this VoltiTECH.
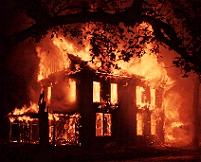